SHARE
MORE DETAIL
In the rapidly evolving world of industrial automation, robotic grippers are becoming essential tools for tasks requiring speed, flexibility, and precision.
To enable accurate control of gripping force and pressure, many advanced systems now integrate a Proportional Regulator — a device that delivers real-time, fine-tuned pneumatic pressure control.
This article explores the crucial role of KaoLu's Proportional Regulators in robotic grippers and how they enhance performance in various industrial applications.
In such scenarios, grip force must be carefully controlled to avoid damaging delicate items or failing to hold heavier parts securely.
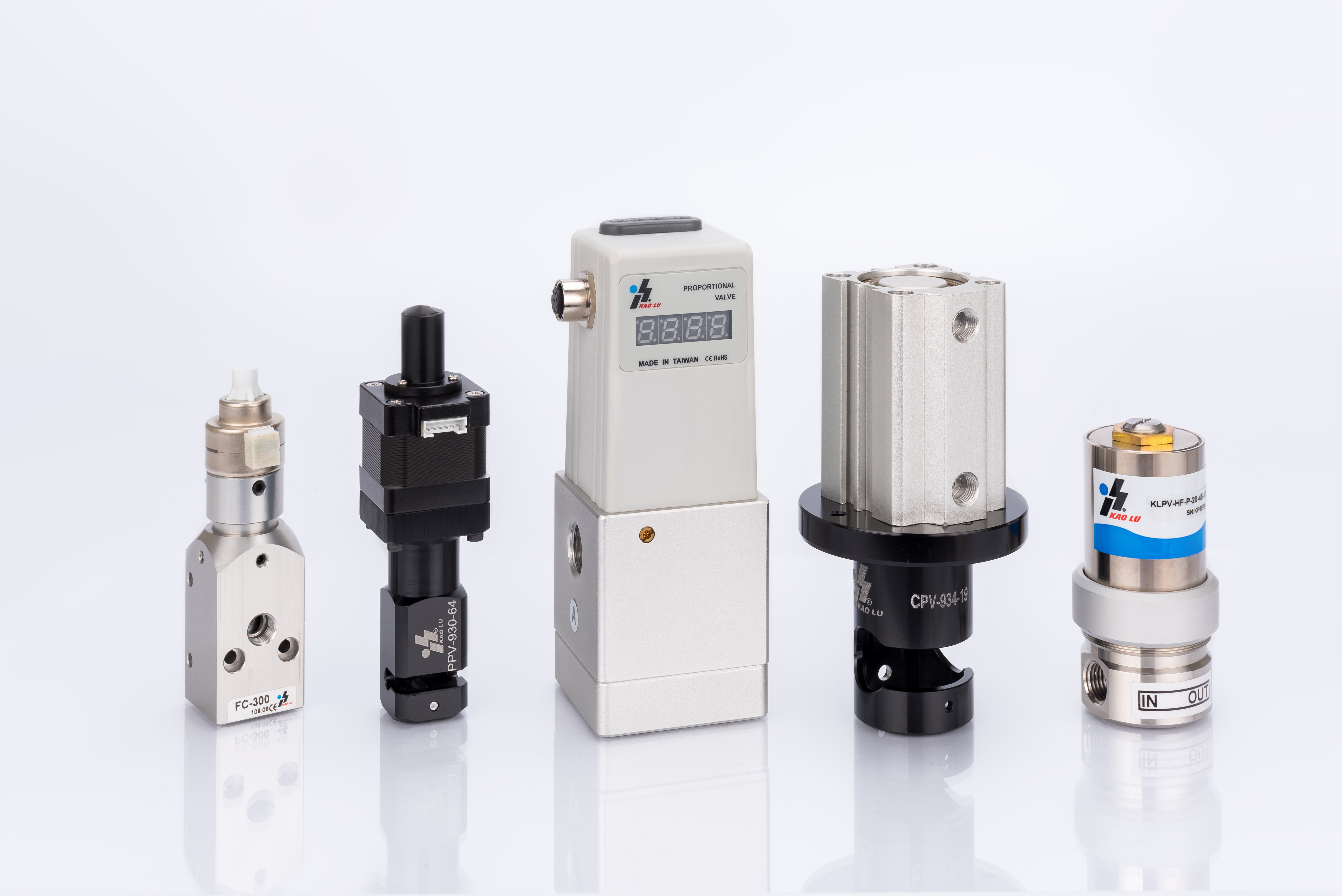
To enable accurate control of gripping force and pressure, many advanced systems now integrate a Proportional Regulator — a device that delivers real-time, fine-tuned pneumatic pressure control.
This article explores the crucial role of KaoLu's Proportional Regulators in robotic grippers and how they enhance performance in various industrial applications.
What is a Proportional Regulator?
A Proportional Pressure Regulator, also known as an electro-pneumatic regulator, precisely controls air pressure in response to an electrical input signal (typically 0–10V or 4–20mA).
Unlike on/off solenoid valves, KaoLu's Proportional Regulator can continuously modulate the output pressure to match dynamic system requirements.
Unlike on/off solenoid valves, KaoLu's Proportional Regulator can continuously modulate the output pressure to match dynamic system requirements.
Why Use KaoLu's Proportional Regulator in Robotic Grippers?
Robotic grippers are tasked with handling objects of varying shapes, sizes, and fragility. In such scenarios, grip force must be carefully controlled to avoid damaging delicate items or failing to hold heavier parts securely.
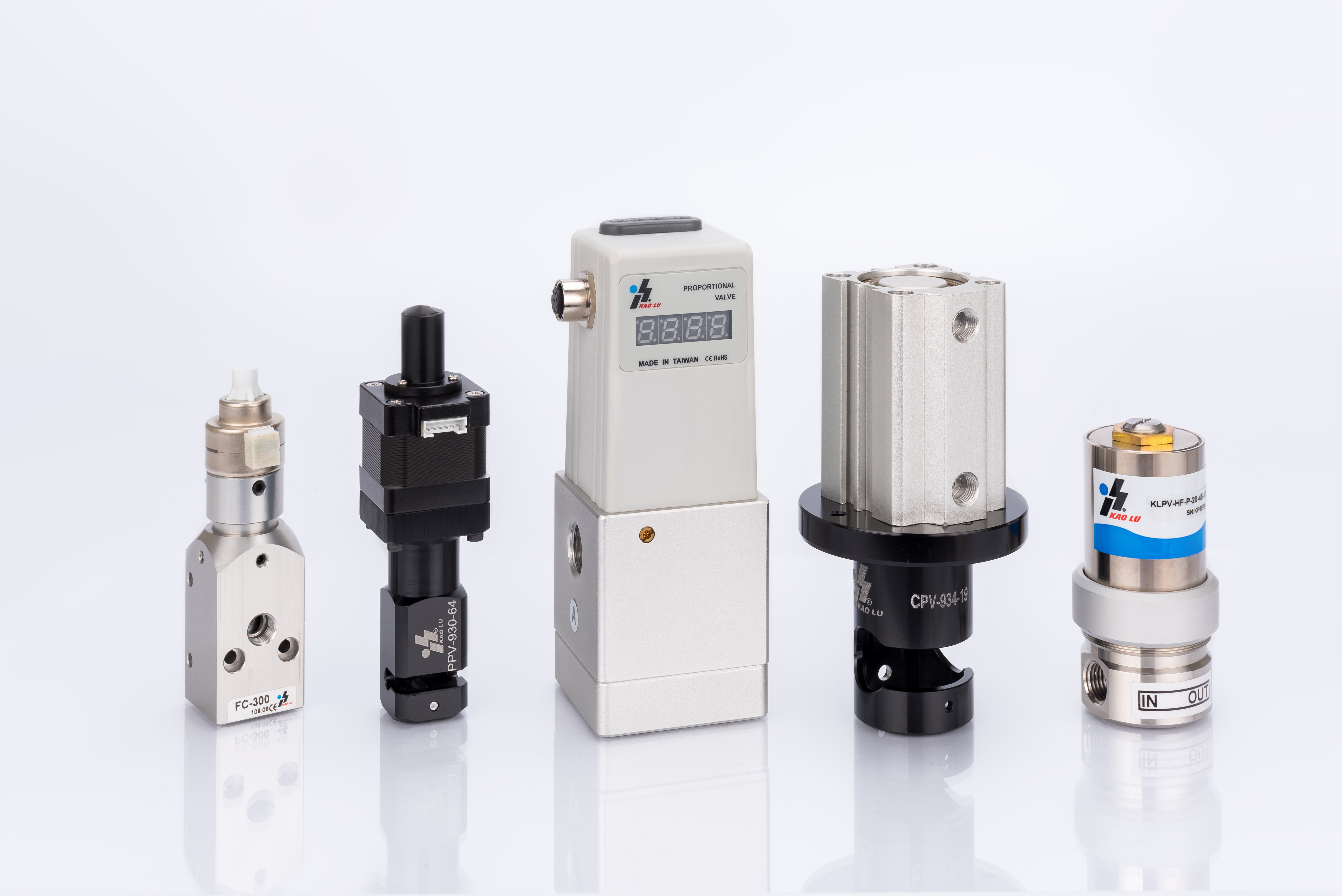
Benefits of Using Proportional Regulators in Gripper Systems:
- Precise Force Control
Proportional regulators enable gradual and responsive pressure adjustment, allowing robotic fingers to apply just the right amount of force for different materials — from fragile glassware to rigid metal parts.
- Enhanced Safety
Soft-touch gripping reduces the risk of crushing or slipping, especially important in collaborative robots (cobots) working near humans.
- Increased Flexibility
With programmable pressure control, a single gripper can be used across multiple SKUs or production lines, accommodating various part geometries and materials.
- Faster Cycle Times
- Repeatability and Accuracy
Digital control ensures consistent and repeatable pressure output, crucial for high-volume, high-precision assembly and packaging tasks.
Common Applications of Proportional Regulators in Robotics
- Electronics assembly – handling circuit boards, sensors, or displays
- Automotive manufacturing – gripping interior trim or sensitive parts
- Food & packaging – automated picking of delicate items like pastries or fruit
- Medical device handling – precise control in cleanroom environments
- Laboratory automation – pipette gripping and test tube transfer
Integration with Robotic Control Systems
Proportional regulators are typically integrated into robot control architectures using:
- Analog input from PLCs or robot controllers
- Digital communication (Modbus, IO-Link, etc.)
- Feedback sensors for closed-loop control
Many modern robotic grippers are now designed with internal pneumatic circuits ready for plug-and-play proportional regulators, simplifying system integration.
Key Features to Look For
When selecting a proportional regulator for robotic applications, consider:
- Pressure range and resolution
- Response time and hysteresis
- Compact size for end-effector mounting
- IP protection rating and vibration resistance
- Compatible I/O and communication protocols
KaoLu's Proportional Regulator is suitable for advanced robotic systems!
Integrating a Proportional Regulator into robotic grippers significantly improves the flexibility, accuracy, and safety of automated handling systems.
As industries shift toward smarter, more adaptive manufacturing, digital pressure control becomes not just beneficial — but essential.
More information about KaoLu's Proportional Regulator, please refer to our website.
As industries shift toward smarter, more adaptive manufacturing, digital pressure control becomes not just beneficial — but essential.
More information about KaoLu's Proportional Regulator, please refer to our website.